Complete Feed pellet line include feed hammer mill, feed mixer, feed pellet machine,cooling machine, packing system. it can make all kinds of animal feed pellet. usually for poultry feed, cattle,cow,sheep. etc.1. Crushing process: The raw materials in the pulverized silo are fed into a pulverizer to be pulverized into powdery raw materials, and then distributed to each batching bin by a conveyor according to the raw material type, and the main equipment is a pulverizer. The purpose of the comminution is to increase the specific surface area of the feed and to improve the utilization of the feed by the animal. Increasing the contact area of digestive enzymes with raw materials, reducing the chewing energy consumption of the animal feeding process, is conducive to improving the feed harvester, and the pulverized raw materials are easily matured in the granulation and tempering stage, and the pulverized feed can be large in the granulation process. The reduction in power consumption can improve the quality and efficiency of subsequent processes.
2. Mixing process: the process of uniformly mixing the ingredients of the batching scale, the core equipment is the mixer, the good mixer can mix the feed evenly in a short time, and the poor mixing opportunity leads to the deterioration of the product quality. Ultimately affect the feeding effect. Mixing should be controlled well, the uniformity is gradually reached the best uniformity with the increase of mixing time, but after mixing evenly and then prolonging the mixing time, the delamination of raw materials will occur. Feeding sequence of the mixer: the raw materials in the formula are added first, then the trace elements are added, the particle size is increased first, and then the particle size is small, the specific gravity is small, and the addition ratio is large, try to avoid delamination: The reason why the chicken material is easy to stratify) The particle size of each raw material in the mixture is close to each other, and the addition of the oil and fat can reduce the delamination of the raw material. Avoid over-mixing, release the product before the optimal mixing time, in order to complete the mixing during transportation, and add anti-layering equipment to the mixing process to minimize the storage time of the product in the silo.
3. Granulation process: The mixed powdery feed is processed into pelletized feed. Feed granulation is easy to digest. During the granulation process, the raw materials of the granules must be stirred for a period of time by a suitable amount of water at a high temperature. The raw materials of the granules are ripened and softened and bonded, and the mechanical energy generated during granulation can increase the raw materials. The degree of damage is easier to digest. If the feed is easier to digest, the animal can absorb its nutrients more quickly and the "meat ratio" will be lower. The taste is good and the taste is good. The pellets have a good scent. The granulation process can also spray other materials on the surface of the granules. The taste is better and the nutrients are more uniform: the ingredients in the formula can be mixed together, so that each granule is Stable nutrients can be achieved, animals can not be selected when eating, and the composition of the formula can use a variety of raw materials. Granulation increases the density of the pellets, and the density of the pellets is increased by the extrusion of the ring membrane, thereby improving the storage capacity of the silo. The pellets have little loss during transportation, and the fluidity is good for transportation and is suitable for the automatic feeding system. Eliminate some viruses because the high temperature kills the toxins in the raw materials, making the pellets safer for animals.
(1) Ring mold granulation:The material with uniform Ripening is firstly removed by the security magnet, and then evenly distributed between the press mixing and the pressing mold, so that the material enters the pressing zone from the pressing zone of the feeding zone, and is squeezed into the die hole by the pressing roller continuously. The columnar feed is formed, and as the stamper rotates, the cutter fixed to the outside of the stamper is cut into a pellet-like feed.
Ripening: The adjustment and treatment of the powder before entering the granular mechanism chamber after the powder is discharged from the mixer. The usual method is to introduce steam into the conditioner to mix and stir the feed and steam. (The Ripening is the key link in the production of pellets, and the effect of Ripening directly determines the quality of the product and the production capacity of the pelletizer)
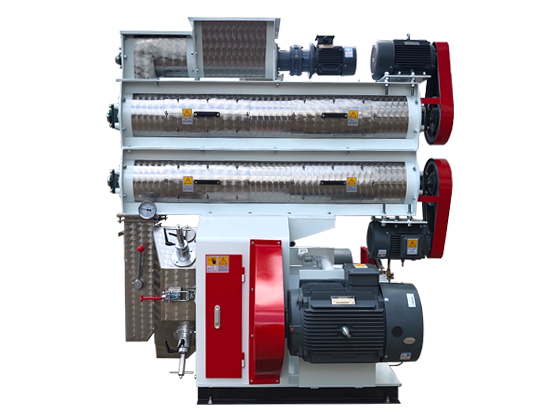
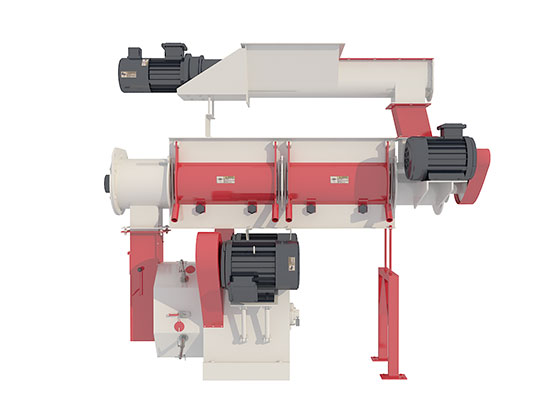
Purpose of Ripening:
1. Gelatinize starch and increase feed digestibility
1. The tempered feed has a certain adhesiveness, which is good for pellet forming.
2. It can soften the feed and play a role in lubrication to improve the life of the ring mold.
3. Eliminate bacteria that are dangerous to animals
4. Improve the moisture content of the particles
5. Reduce energy consumption by 10% and 20% and increase production efficiency
The ideal conditioning effect:
The temperature reaches 82C-88C and the moisture reaches 15.5%-17%. The quenching room needs 30-45 seconds of residence time.
(2) Flat mold granulationThe mixed material enters the granulation system, and the rotary hopper located at the upper part of the granulation system evenly spreads the material on the surface of the die, and then presses the material into the die hole by the rotary press mixing and presses it out from the bottom. The rod-shaped feed coming out is cut into the required length by a cutting roll.
4. Cooling: During the granulation process, a large amount of heat is generated due to the introduction of high-temperature, high-humidity steam, and the material is just discharged from the granulator, the water content is 16%-18%, and the temperature is as high as 75 C-85C, under these conditions, the pellet feed is easily deformed and broken, and it will also cause sticking and mildew during storage. It must be reduced to below 14% and the temperature is lowered to 8 °C below the temperature. This requires cooling.
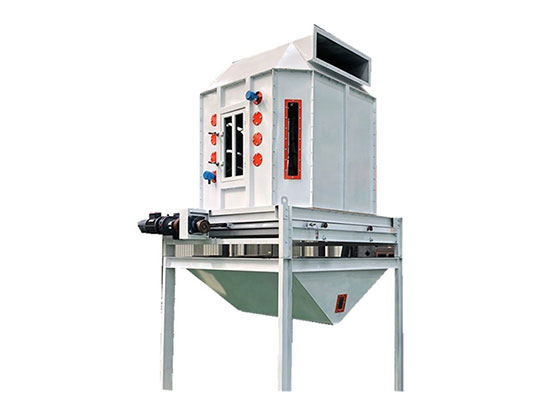
5. Crushing: In order to save electricity, increase production and improve quality in the production process of the particle machine, the material is first made into particles of a certain size, and then crushed into qualified according to the particle size of the livestock and poultry.
6. Screening: After the pellet feed is processed by the pulverization process, some powder clots and other materials that do not meet the requirements will be produced., the crushed pellet feed needs to be sieved into products with uniform granules and uniform size.
7. Finished packaging process: The process of weighing, bagging and slitting the finished product by automatic packaging equipment. Generally, the finished products are shipped in two forms: bulk and bagged. Due to the restrictions of transportation equipment and large-scale feeding, the bagging method is often adopted. The automatic weighing system can weigh different feeds according to customer needs.