Different livestock have different requirements on the size of the pellets in different growth stages. The roller crusher is a special equipment for breaking large particles into small particles. For example, if the granulator directly presses small particles, the result is low yield and high energy consumption. Compared with crushing large particles and then crushing into small particles by a pelletizer, this can maintain large output and only increase the crushing power consumption. Compared with small particles, the output can be increased by 3-4 times, and the energy consumption is reduced by 2-3 times, so it is an indispensable device in the granulation section. Generally, large particles of φ4.5-6 mm are pressed and crushed into 0.7-1.5 or 1-2.5 small particles by the machine.
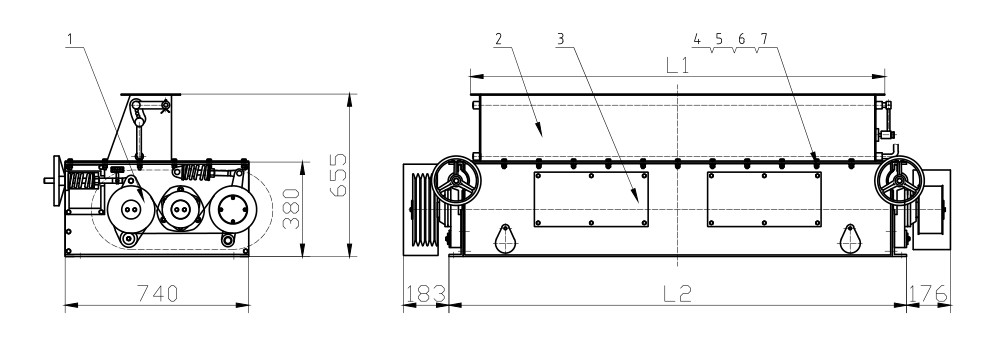
1. Right wall panel part 2. Upper cover part 3. Lower housing part 4. Bolt 5. Nut 6. Flat pad 7. Spring pad 8. Motor drive part
Crushed granules: The working process is that the pressed granules are cooled by the cooler and then enter the granulator inlet. After the shutter has been opened, the rolls are fed into the two rolls. The rolls are divided into fast and slow rolls. The surface of the rolls has grooves, which pass through two rolls. Particle extrusion and differential shearing are broken, and the degree of fracture is related to the rolling gap.
The roller type feed pellet granulator is a device for crushing feed granules. The twin roll feed particle crusher is suitable for crushing poultry feed such as chicken feed, duck feed and goose feed.
The double roll structure has a simple structure and low cost.
The three-roller structure enables the granulator to work in a balanced continuous state with uniform particle size and higher crushing efficiency.
The flap is configured to adjust the size of the inlet and the feeding is more uniform
Low graded return, high yield, equipped with feeding mechanism, stepless adjustable, low energy consumption.